This post’s subject is the turbofan jet engine. It’s used in every commercial airplane due to high thrust and for being the most efficient and silent type.
Operation principle of turbofan jet engine
Air entrance
The turbofan has this name due to the big propeller which sucks air. Each blade has an aerodynamic shape, when wind arrives at the blade, a lift force is induced, like in airplane’s wing. This force on blades is the one that contributes more to plane’s thrust with turbofan engines.
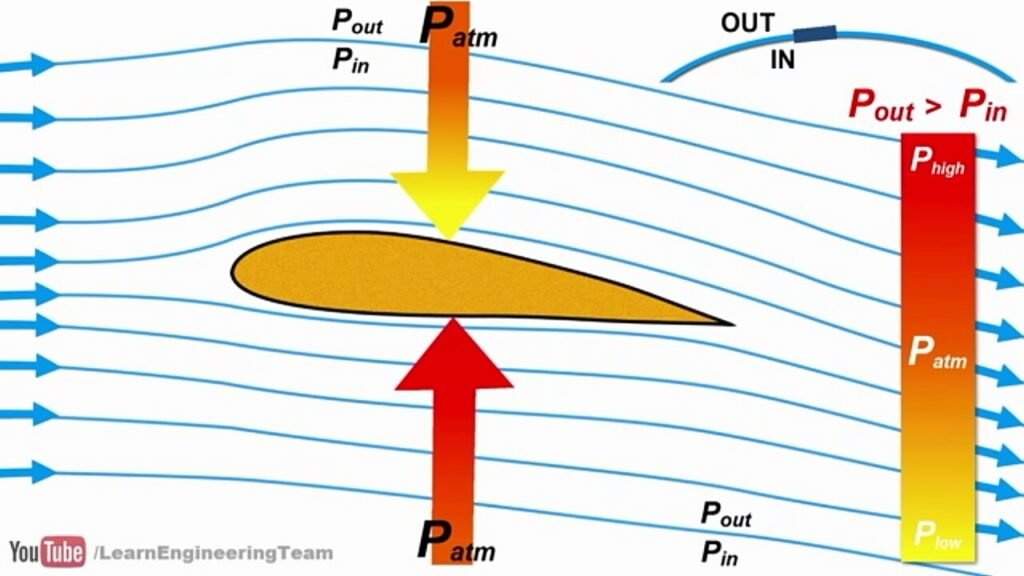
When higher the propeller, higher the capacity to suck air to the motor.
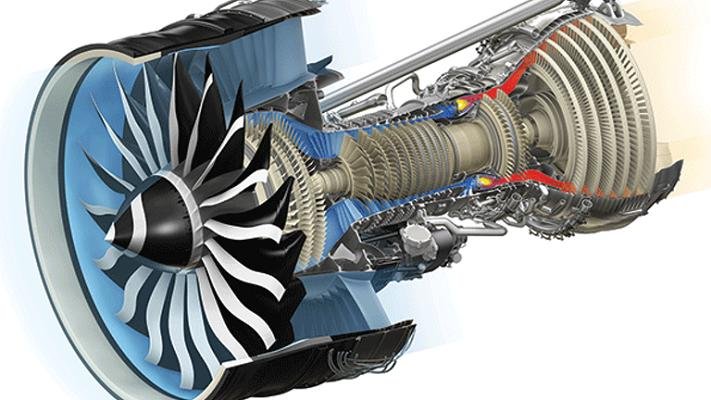
Air compression
To execute combustion in the engine, air must have high pressure and temperature. Right behind the fan, there is a low pressure compressor, and then, another compressor of high pressure, that spins faster than the previous one.
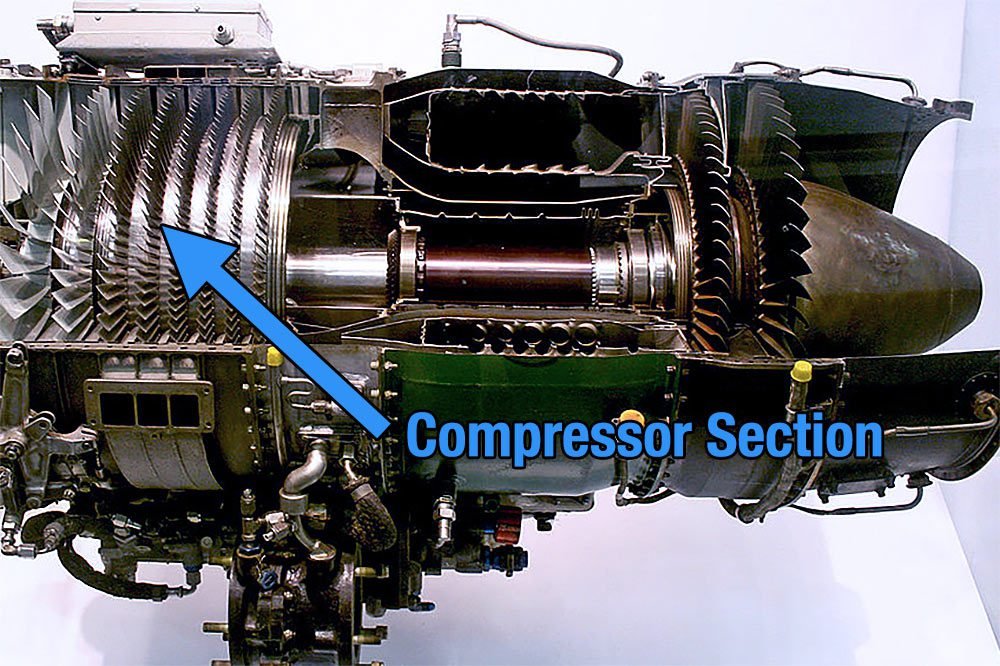
Are used 2 types of compressors: axial and centrifugal. In axial type, the blades have airfoil shape and the air flow parallel to the engine’s shaft.

An axial compressor has 1 or more stages of fixed blades, called stators. The stator’s function is to convert rotational energy in pressure and directs the flux to the next stage in rotation, called rotor.

Combustion
After passing through compressors, air pressure and temperature become much higher. The next stage is the combustion chamber.
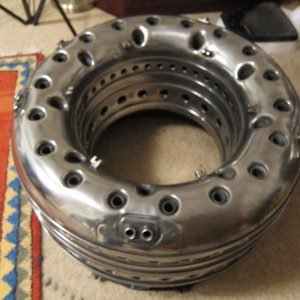
The fuel goes from tank to the chamber by valves and a tube, aided by pumps. Many fuel injectors put fuel on the chamber like a spray, to mix with high pressure and high temperature air. An electric spark by igniter initiates the mixture’s combustion.
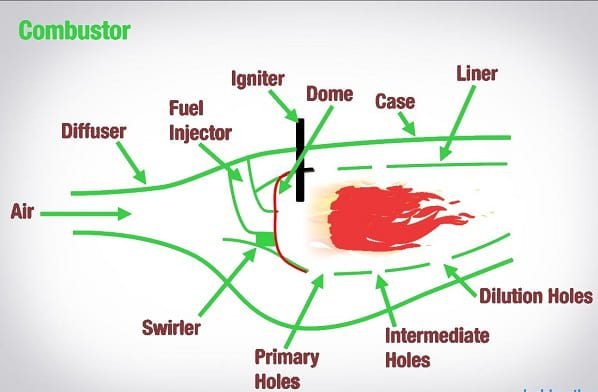
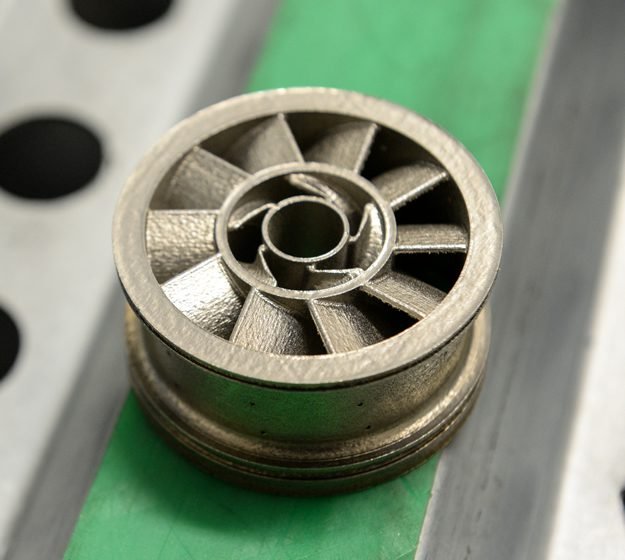
The first part of “All fuels” show the fuels used in aviation.
Turbines
The gases coming out of combustion chamber go to high-pressure and low-pressure turbines respectively. These turbines use kinetic energy of gases to spin the compressors and the fan, because they are all linked to the same axis.
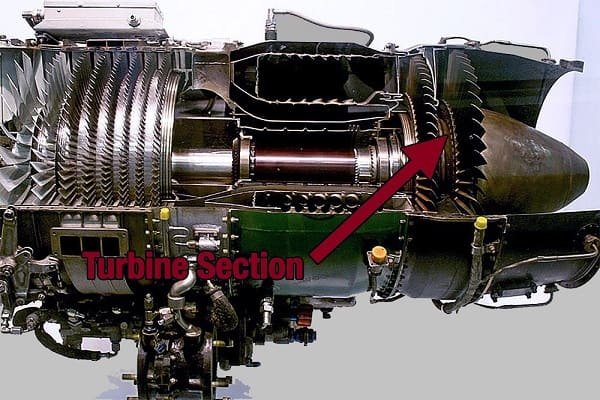
Low pressure blades are longer, a lower speed reduce the centrifugal stress on blade’s base, increasing it’s lifespan.
Exhaustion
After passing through turbines, the gas mixture is expelled by a nozzle. It must be narrow to increase airplane’s thrust. It’s an application of Newton’s third law, when the hot air is expelled through the nozzle at high speed, a force is produced. Air generates a reaction force which produces thrust to the plane.
The equation of turbofan thrust force , in Newtons (N).
- , the bypass air flux rate.
- , speed of bypass flux.
- , air speed before entering the engine.
- is the air flux rate that passes inside the engine.
- is the air speed expelled by the nozzle.
Turbofan bypass rate
Most of air sucked by the big fan doesn’t go to combustion chamber, but to the side of engine. This is called bypass flux.
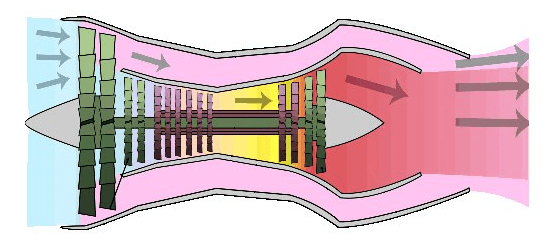
Equation of bypass rate.
The 2 turbofan categories are: low-bypass and high-bypass. The high-bypass has a big air volume that pass by, in comparison to volume that enters in the engine. On low-bypass, rate between the fluxes is smaller.
