This post’s subject is the work envelope on robotics. Manipulator robots are classified according to this important concept.
What is a work envelope?
It’s a space with geometrical shape where the manipulator robot can operates. Depends on the degrees of freedom, robot size, types of actuators and range of end effect, part of robot that interacts with the environment, like for example, a claw.
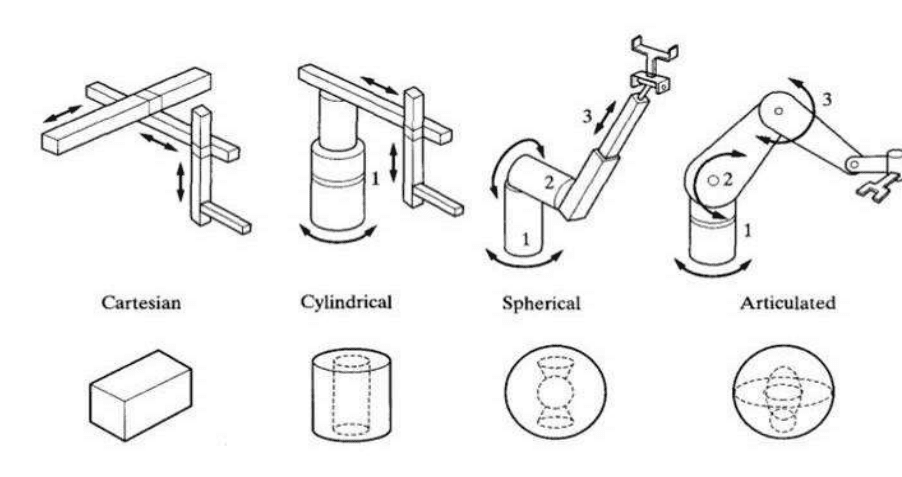
The importance of work envelope
The work envelope determines the best application to the robot. When choosing or design a robot for a task, must be defined the shape and size of work envelope in the operation spot. In some situations, the envelope must be limited by sensors that send signals to the controller to avoid accidents.
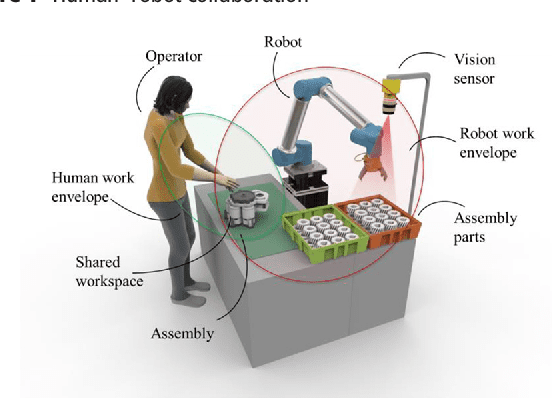
Classification of industrial robots and the work envelopes
Cartesian or gantry robots

They move in Cartesian coordinates x, y and z. All actuators must be linear. Therefore, the work envelope will be a parallelepiped. The Cartesian robots have the simplest control.
Cylindrical robots
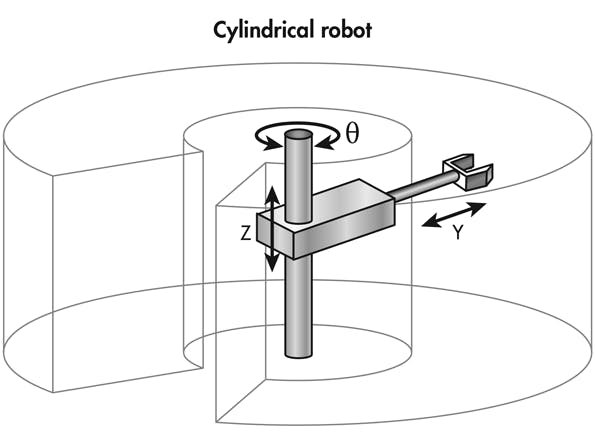
If the base joint is rotational, the manipulator moves on cylindrical coordinates.
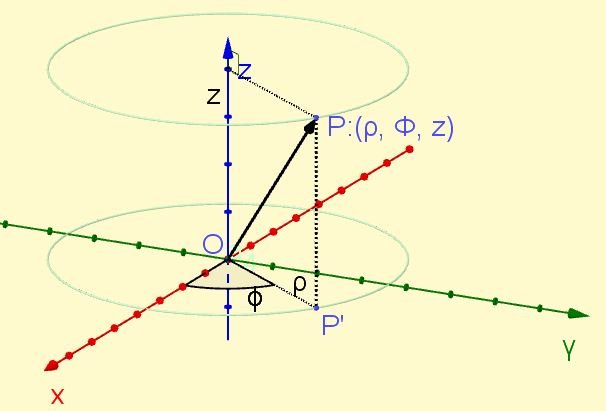
This type of robot has a dead zone, where it can’t operate due to size and motion limitation of linear actuator. This dead zone is inside the work cylinder.
Polar or spherical coordinate robots
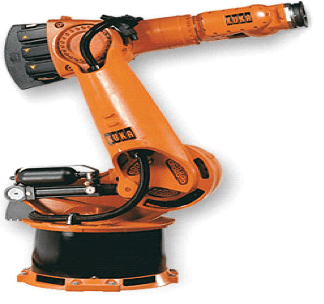
With 2 rotational and one linear actuators, the robot moves on spherical coordinates.
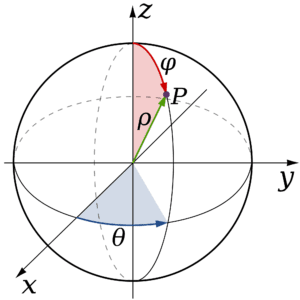

Articulated robots

All articulated robot’s actuators are rotational. The dead zone is smaller than that of spherical robot, in relation to work envelope.

SCARA
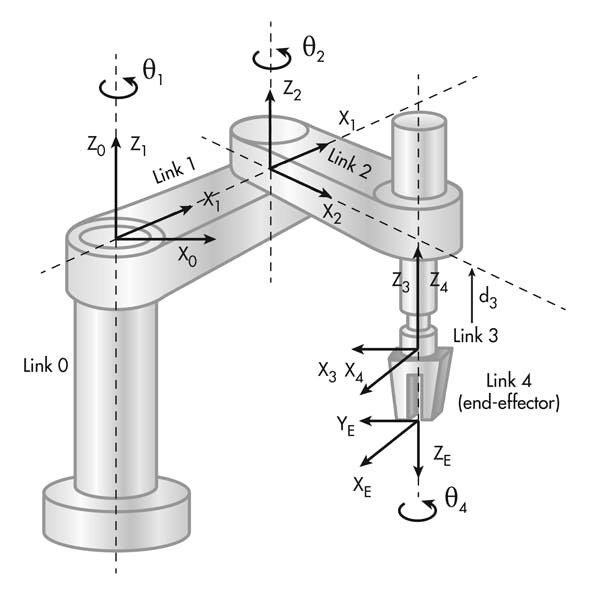
It’s the abbreviation of Selection Compliance Assembly Robot Arm. Has two rotative actuators and a linear one, as in polar configuration, the linear joint operates on vertical.
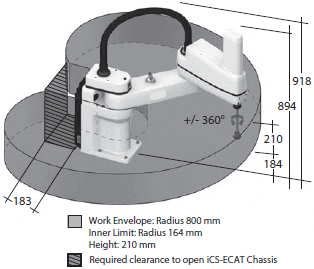
Delta
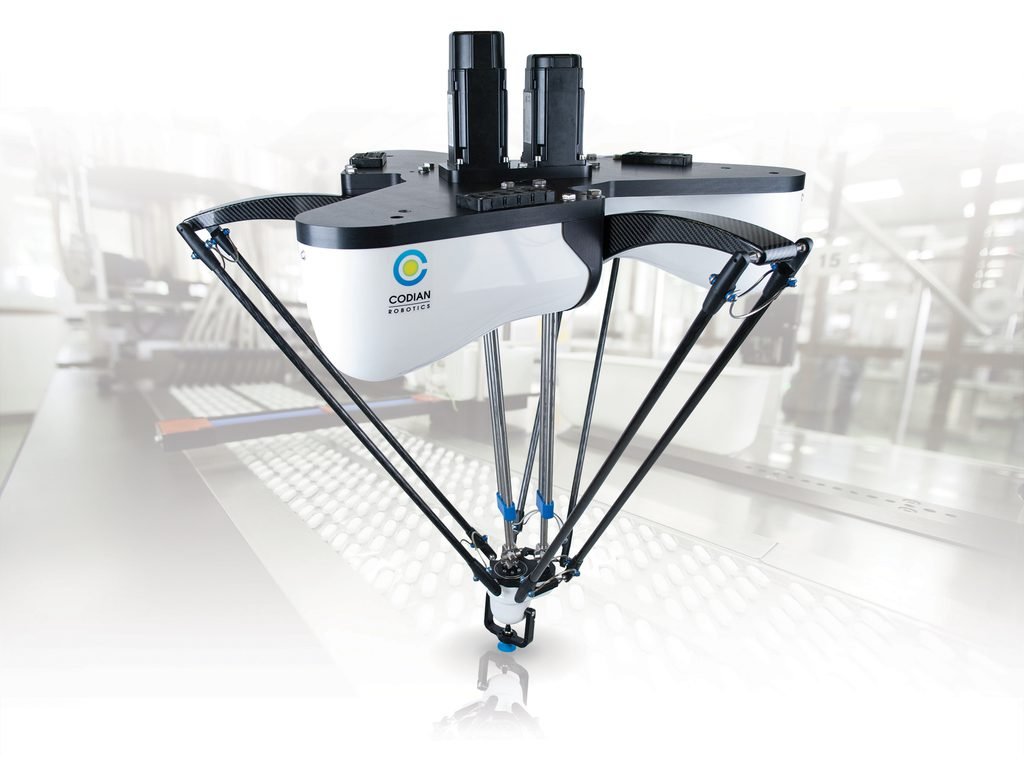
This type is used to pick up and put small objects at great precision and speed. Has 3 articulated parallelograms connected to a fixed platform and driven by motors that are 120º from each other. The end effector is linked to a mobile platform. The work envelope is half of a sphere. The following video shows how a delta robot moves.